The New US Tariffs
A Trade Shift Reshaping Global Markets
By Amna Kanwal

The global economy thrives on the seamless movement of goods and services across borders, creating a network of interdependent markets. Free trade agreements, low import duties, and international collaborations have historically driven economic growth and innovation. However, when a major economy like the United States imposes tariffs and additional taxes on imported goods, it disrupts this balance, triggering cost increases, shifting supply chains, and sparking geopolitical tensions.
Recently, the U.S. announced a new wave of tariffs targeting key industries, particularly electric vehicles (EVs), semiconductors, and steel. These measures, aimed at curbing reliance on Chinese imports and strengthening domestic manufacturing, signal a shift toward economic protectionism. While the tariffs offer potential advantages for American manufacturers, they also introduce significant challenges for businesses, consumers, and global supply chains.
The question remains: How will these new tariffs reshape international trade and impact global economic stability? To answer this, we must explore the rationale behind these trade policies, their consequences for industries and nations, and the strategies businesses must adopt to stay competitive.
Understanding U.S. Tariffs: A Business Perspective
Governments impose tariffs for various reasons, often to support domestic industries and address trade imbalances. The latest U.S. tariff adjustments primarily target China’s dominant industries, including EVs, batteries, and semiconductors, with the most significant move being a 100% tariff on Chinese EVs.
This dramatic increase is intended to limit the influx of low-cost Chinese vehicles into the U.S. market, protecting American automakers from aggressive pricing competition. Additionally, tariffs on steel, aluminum, and semiconductors signal a broader effort to encourage domestic production and reduce reliance on Chinese manufacturing.
The primary objectives behind these tariffs include encouraging domestic growth, adjusting the trade balance, and diversifying supply chains. Tariffs shift demand toward local manufacturers by making foreign goods more expensive, promoting industrial expansion and job creation. The U.S. aims to reduce its long-standing trade deficit with China, which has persisted for decades, by making imported goods less attractive.
This move also incentivizes businesses to rethink their reliance on Chinese suppliers and explore alternatives in India, Mexico, and Southeast Asia. While these measures are designed to strengthen U.S. manufacturing, they also create cost pressures for companies that rely on global supply chains.

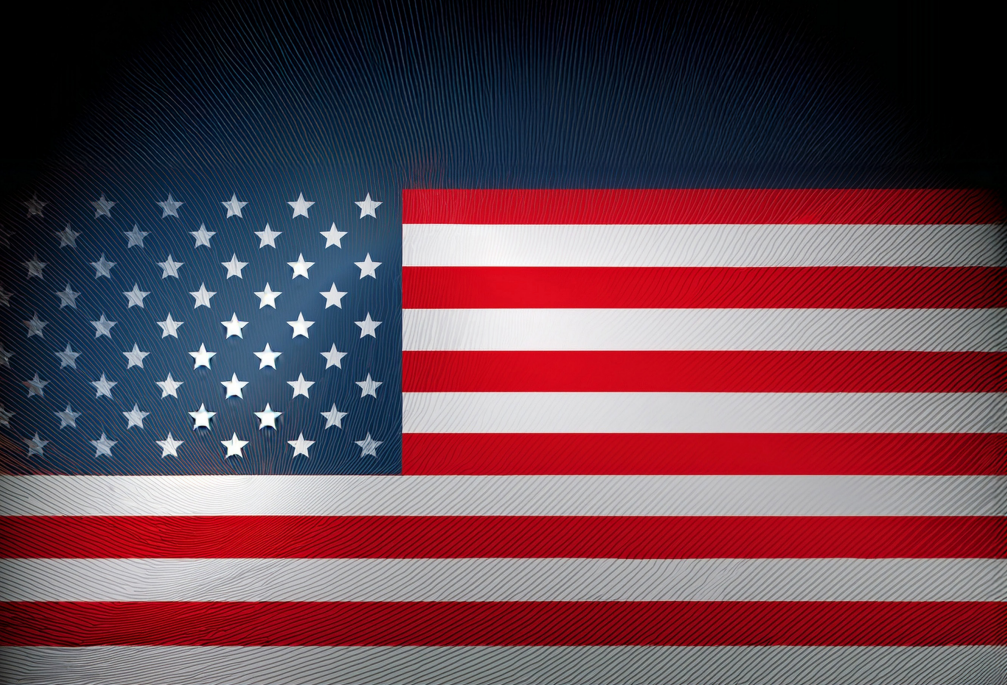
However, these tariffs also introduce new challenges for businesses that depend on international trade. Higher import costs for raw materials and components could increase production expenses, forcing companies to adjust pricing strategies.
Manufacturers reliant on Chinese supply chains may either absorb these additional costs, which could impact profit margins, or pass them on to consumers, potentially reducing product demand. Small and mid-sized businesses, in particular, may struggle to navigate these rising costs compared to larger corporations with diversified supplier networks.
On the other hand, these tariff adjustments could accelerate investment in domestic manufacturing and supply chain resilience. Companies may look to expand operations within the U.S. or seek partnerships with suppliers in tariff-free regions.
While shifting production closer to home requires significant investment, businesses that adapt early may gain a competitive advantage in the long run. As companies reevaluate sourcing strategies and explore new markets, industries could see shifts in global trade patterns, fostering innovation and long-term economic stability.
Key Industries Affected
The electric vehicle sector is one of the most heavily impacted industries, as the U.S. government imposes a 100% tariff on Chinese EVs. This makes it nearly impossible for Chinese automakers like BYD and Nio to compete in the American market. While this protects American manufacturers such as Tesla, Ford, and General Motors, it also limits consumer choice and could lead to higher vehicle prices.
The tariff also affects battery production, as many U.S. automakers source lithium-ion batteries from Chinese suppliers. This additional cost burden prompts manufacturers to seek alternative sources in South Korea, Japan, and even domestic battery production facilities to avoid the increased costs.
The semiconductor industry is another key target of the new tariffs, with restrictions on China-made chips and components. The semiconductor market is a crucial part of the global tech industry, with companies like Apple, Intel, and Qualcomm depending on affordable and efficient chip production. With tariffs in place, production costs are expected to rise, leading to potential delays in product releases and increased consumer prices.
Major semiconductor industry players are ramping up investments in U.S.-based chip production to counter these challenges. Companies like TSMC and Intel are leading the charge in reshoring semiconductor manufacturing, while countries like India and Vietnam are positioning themselves as alternative supply chain hubs.
The new tariffs significantly affect the steel and manufacturing sector, with implications reaching beyond raw materials to industries like construction, infrastructure, and industrial production. Higher costs for steel and aluminum will likely increase expenses for automobile production, machinery, and appliances.
Businesses in these industries may need to either absorb these costs or pass them on to consumers, leading to price hikes across multiple sectors. This creates a ripple effect throughout the economy, forcing manufacturers to reevaluate their supply chain strategies and seek cost-efficient sourcing solutions.
Global Business Adjustments
The new tariffs don’t just affect China; they create market-wide shifts that influence Europe, Latin America, and emerging economies. European automakers like BMW, Volkswagen, and Mercedes-Benz, which have a strong presence in the U.S. market, are now facing higher costs due to tariffs on steel and automotive components.
This could lead to price adjustments on European vehicles sold in the U.S. or a strategic move to increase North American production to bypass import taxes. Companies that rely on Chinese-manufactured parts for their vehicles may be caught between rising costs and needing to remain competitive in the American market.
Emerging markets such as India, Mexico, and Brazil stand to gain from the global realignment of supply chains. With businesses actively seeking alternatives to China, these countries are positioning themselves as attractive investment destinations. India, for example, is ramping up its semiconductor manufacturing capabilities, with major global players investing in chip production facilities.
Benefiting from the USMCA trade agreements, Mexico is becoming a key player in automobile and electronics manufacturing, offering U.S. companies a cost-effective alternative while maintaining proximity to American markets.
Asian markets beyond China are also adjusting to the shift in global trade dynamics. Countries like Vietnam, Thailand, and Indonesia are emerging as viable manufacturing hubs, particularly electronics and consumer goods. With Chinese manufacturers facing higher tariffs, multinational companies increasingly diversify their supply chains to these regions.
This transition reduces exposure to the U.S.-China trade tensions and allows businesses to take advantage of lower labor costs and favorable trade agreements. Expanding infrastructure and government incentives in these nations further support this shift, making them competitive alternatives for companies seeking stability amid rising protectionism.
At the same time, global logistics and shipping industries are feeling the ripple effects of these adjustments. Companies that once relied on China as a central production hub must now reconfigure shipping routes, warehouse locations, and distribution networks. This restructuring may lead to temporary inefficiencies and increased freight costs as businesses establish new supply chains.
However, these changes could foster greater diversification and resilience in the long term, reducing reliance on any single market. As global trade patterns evolve, businesses that can quickly adapt and leverage emerging markets may find new opportunities for growth despite the challenges posed by tariffs.

Market Reactions & Economic Trends
The new tariffs have triggered various market reactions, with businesses, investors, and consumers adjusting to the changing trade landscape. One of the most immediate effects has been supply chain adjustments, as companies seek to reduce their dependence on China. Major corporations are increasing their focus on regional manufacturing, leading to higher investments in U.S.-based production and partnerships with suppliers in countries like Vietnam, South Korea, and India.
Financial markets have also responded to the tariff announcements with short-term volatility. The S&P 500 and Nasdaq experienced declines following the announcement, reflecting investor concerns over rising business costs and potential inflation risks. Historically, trade restrictions have led to market fluctuations, and this latest wave of tariffs is no exception. As companies adjust their strategies, stock market trends will shift based on how businesses manage increased production costs.
Consumer prices are another concern, as rising import costs often lead to higher retail prices. Past tariff implementations, such as those introduced during the 2018-2019 U.S.-China trade conflict, resulted in a 15% increase in household expenses. If these new tariffs persist, consumers could see price hikes on electronics, vehicles, and industrial goods, further straining household budgets.
Financial markets have reacted with characteristic volatility. The S&P 500 and Nasdaq experienced declines following the announcement, reflecting investor uncertainty over potential economic slowdowns and rising production costs. Sectors directly affected by tariffs, such as automotive, semiconductor, and consumer electronics, saw sharper declines as analysts revised earnings forecasts to account for increased expenses.
The bond market has also responded, fluctuating treasury yields as investors weigh the long-term impact of trade restrictions on inflation and economic growth. While some industries may experience short-term turbulence, others, such as domestic manufacturing and logistics, could see increased capital inflows as businesses adapt to new trade dynamics.
For consumers, higher import costs may translate into noticeable price hikes across multiple sectors. Past tariffs, including those imposed during the 2018-2019 U.S.-China trade dispute, resulted in a 15% increase in household expenses, affecting everything from electronics to home appliances.
If the current tariffs remain in place for an extended period, industries dependent on Chinese imports, including automobiles, consumer electronics, and industrial machinery, may be forced to pass on the costs, leading to inflationary pressures. However, some companies may opt to absorb a p
Business Strategies for Navigating the Changes
As businesses face evolving trade policies, adapting quickly and strategically is critical to maintaining market competitiveness. Supply chain diversification is one of the most effective ways to mitigate risk. Many companies are shifting manufacturing and procurement beyond China, with India, Mexico, and Vietnam emerging as key alternatives. These regions offer competitive labor costs, expanding industrial infrastructure, and trade agreements that provide tariff advantages. Additionally, some businesses are exploring “nearshoring” strategies, bringing production closer to their home markets to reduce dependence on long-distance supply chains.
Cost management and pricing strategies will also play a crucial role. Companies must decide whether to absorb additional costs, adjust product pricing, or renegotiate supplier contracts to maintain profitability. Businesses with strong brand loyalty and high-margin products may have more flexibility to increase prices. At the same time, those in price-sensitive industries may need to focus on efficiency improvements to offset tariff expenses. Automation and digitalization are also becoming more critical as companies invest in AI-driven supply chain management, robotics, and smart manufacturing to lower operational costs and enhance efficiency.
Another key strategy is proactive market monitoring and policy adaptation. Businesses that stay ahead of trade policy shifts and economic trends can make informed decisions about expansion, investment, and product development. Companies that rely heavily on imports should closely track tariff negotiations and potential trade agreements, allowing them to adjust sourcing strategies before new restrictions take effect. Some businesses may also explore lobbying efforts and industry coalitions to advocate for favorable trade policies that minimize disruptions to global commerce.
In a rapidly changing trade landscape, businesses that remain agile and innovative will be best positioned to thrive. While tariffs introduce new challenges, they also create opportunities for companies willing to rethink supply chains, optimize operations, and explore new markets. By leveraging strategic planning and investment in long-term solutions, businesses can navigate economic uncertainty while maintaining a competitive edge in the global market.
Conclusion: A Transforming Trade Landscape
While the new U.S. tariffs aim to strengthen domestic industries, they also reshape global trade dynamics. To stay competitive, businesses must navigate higher costs, shifting supply chains, and evolving market conditions. Companies that can successfully adapt by leveraging regional partnerships, diversifying suppliers, and adopting cost-efficient production strategies will be best positioned to turn trade disruptions into new opportunities.
The trade landscape is evolving, and companies that proactively adjust their strategies will be the ones that thrive in this new economic environment. Whether through reshoring, forming strategic alliances, or optimizing supply chain networks, businesses must remain agile in response to these global trade shifts.